There are currently more than 7,000 tons of high-level nuclear waste (HLNW) in Pennsylvania alone—most of which is composed of spent nuclear fuel. That is about 1,000 elephants of nuclear waste in just Pennsylvania!
The high level of radiation and heat given off from this waste makes it particularly problematic to store safely. Hence, there are no permanent repositories for HLNW in the U.S. In addition, the current design of repository structures to safely contain, isolate, and dispose of HLNW (such as heat-generating spent nuclear fuel) is limited in part by the materials available to construct these special structures. Our research team, the Responsive and Adaptive Infrastructure Materials (Re-AIM) laboratory, in collaboration with the BEAM and Arguelles research groups, is working on producing new and better materials to act as a buffer that can prevent any spillage of harmful radioactive materials and safely store HLNW.
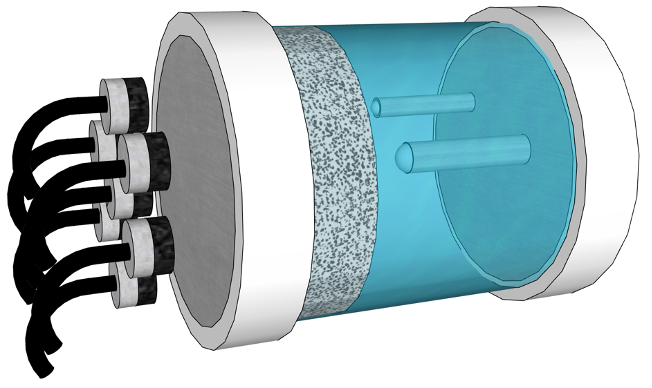
In the typical design of permanent storage of HLNW, the waste is first vitrified (turned into glass) and sealed into a metal canister. These canisters are placed deep within geological formations (almost two Empire State Buildings deep!) and surrounded by a buffer material. The buffer material can help protect the metal canister containing the harmful HLNW by slowing the natural corrosion of the metal. It also slows the movement of and captures any radioactive material that may leach out of the waste container if it corrodes.
One popular choice for a buffer material is bentonite clay. However, at temperatures above 100°C, one of the components of bentonite clay (montmorillonite) is irreversibly transformed, and the capacity of this sponge-like material to swell and protect HLNW canisters is reduced. To prevent this detrimental transformation, costly practices have been adopted, such as surface storage of spent nuclear fuel packages, which requires 200-540 years for the nuclear waste to cool to acceptable levels where they will not overheat the bentonite clay. Thus, there is a real need to develop new buffer materials that can enable robust repository designs.
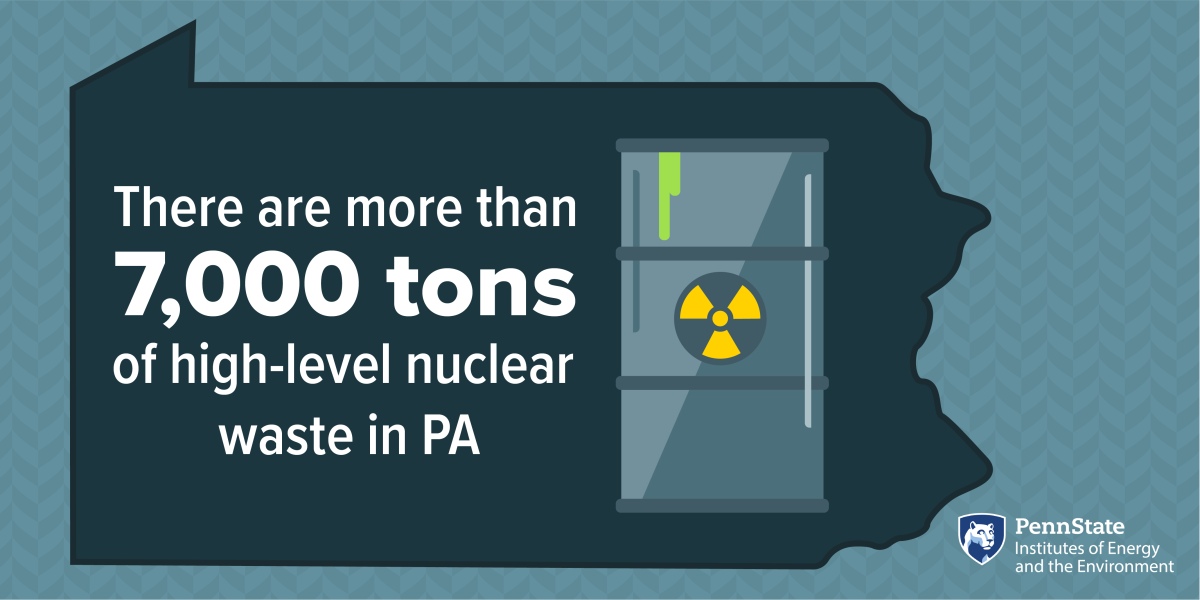
We are focusing our search for a better buffer material on cementitious magnesium aluminophosphates (Mg-Al-P). This class of materials has the potential to provide an environment around nuclear waste packages that significantly reduces the corrosion of metal canisters. We are also interested in engineering these cementitious Mg-Al-P to be specialized sponges that can immobilize fugitive radioactive material over geological timescales (more than 1 million years) in a worst-case scenario that could occur if the metal canister is punctured by a natural hazard or human activity. Mg-Al-P tends to be stable to higher temperatures than current buffer materials, allowing for HLNW to be deposited in geological repositories earlier than is currently possible with bentonite clay. While many buffer materials are only suitable for use in a few geological formations, the material we are developing will be suitable for use in many different geological formations such as salt, crystalline rock, or clay/shale repositories.
To optimize the designed buffer material, a deeper understanding of how the properties of cementitious Mg-Al-P materials change with changes in chemistry needs to be developed. We will use various experimental methods such as x-ray diffraction, thermal gravitational analysis, and pore-solution chemical analysis assessment to develop a detailed understanding of how to tune the MG-Al-P material to give the best performance as a buffer material for nuclear waste. To understand the interaction between the buffer cement that we develop and the steel of the waste canisters, we will use an array of ultrasonic sensors to observe the possible corrosion that could occur.
Because HLNW remains hazardous for such a long time, the experimental measurements made over short time scales are not enough on their own to guarantee performance over geological time periods. To understand how the buffer material will perform over a long time, the experimental data collected will be used to create a computer model that can simulate how the new buffer material acts over long time periods.
While better long-term storage of nuclear waste is the focus of this project, much of what we learn from this project will be directly applicable to creating longer-lasting infrastructure and reducing carbon emissions. A major cause of failures of steel-reinforced concrete structures is corrosion (rusting) of the steel. The cementitious Mg-Al-P that we are developing to protect the steel of waste containers from corrosion also has the potential to save the steel rebar from corrosion if used to replace portland cement in concrete in other civil engineering structures. This is an important feat because the production of portland cement is an energy-intensive process, which releases large quantities of carbon dioxide due to carbon dioxide being released from limestone as it is turned into quick lime (about 6% of global carbon dioxide emissions). Cementitious Mg-Al-P does not contain quick lime. Therefore, the manufacturing of Mg-Al-P has the potential to have a smaller carbon footprint than portland cement.
Ultimately, this project will make significant strides to advance the robust design of the U.S. and global nuclear waste disposal infrastructure with greater capabilities to isolate and contain nuclear waste.